We hopped into the car and made a list of needs. First on the list was hardware: trucks, barrings, wheels, grip tape, and risers. Second on the list was more wood of course! Third was resin, or sealant, or something to protect the wood. Fourth, which quickly turned into First, was breakfast. And Fifth was left open for changes that we would encounter as we progressed through the day.
Our first stop at the local skate shop quickly sent us along to another shop, learning that not all shops carry 'longboard hardware.' Breakfast burritos where along the way and Starbucks too. We walked into Peter Glen Snow and Skate in time to meet the new employee who knew nothing about skating and the old employee to touted to know everything about skating, neither had a sense of humor, but according to some schools of thought, both had style. In an attempt to test their knowledge and to pick their brains a bit we asked as many questions we could including ones we knew the answer to already. The passed almost every test and we walked out $110 less with our hands full of semi-high end hardware for just one board. ... we learned that they sell boards on consignment and that had the glorious effect of lifting our spirits to the next possible degree. Who could have known we'd get so high within so little time.
A quick stop into the local art shop in search of wood left us a little slower in our stride but simultaneously with information to lead us further down our trail of construction.
Woodworks is about 12 miles up the road. If you were to imagine any good in the world that comes from wood, I sure it's originations are in places like this. Filled with toys, tools, ideas, and passion, it has little to initially bore it's customers. Jesus would have been just another hack in this place. To the right stood drill presses, band saws, and table saws, shiny, metallic, clean. To the left hung lathes and awls for every size imaginable. Ahead were the isles, so carefully stocked and organized that it was useless to wander through them unless time was your leisure and once you found the isles you needed, no further was you next need that just behind you. This place was amazing. I felt the money pouring out of my wallet, through my pockets, and into their registers... I couldn't stop it.
We were directed to the back corner of the store where they kept their hardwoods in the sizes and quantities we wanted. Our jaws dropped with the assortment... with the opportunity.... with our vision.
...
...
It took some time before I could regain a realistic outlook on life, benching the rotating images of zebra wood, purple heart, and ebony.
I had scribbled some ideas for names on a piece of paper earlier that morning.
The drive back from WoodWorks filled us with inspiration and a name had arrived. We got back to the palapa and as if by fate paper was strewn across the ground and the names I had put there were face down in the dirt. Names that would never make it to the boards, "Mizell Designs," "101 boards," "Palapa Built," "JPM Boards," all deceased. The drive home had given ample time to explore new names and from my mind was dug up "Boojum." Boojum, the tree of the Sonoran Desert, of the middle land of baja surf, one prize within the University of Arizona's Cactus Garden. Boojum's subtly exist in many manners in my life as a positive yet reserved. Always appreciated, available if searched for, missed if gone. And so now it is the choice for the board company and will Boojum's will enjoy some exposure.
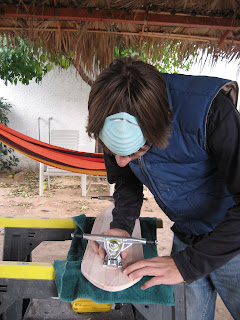
Back home we started moving on the boards again. We positioned the trucks and drilled the boards. Designed the logo for Boojum Boards and signed each one.
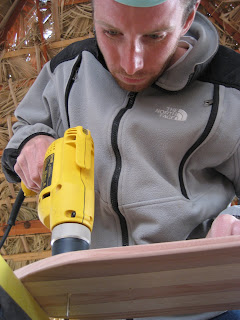
We mixed and applied our expoy resin.
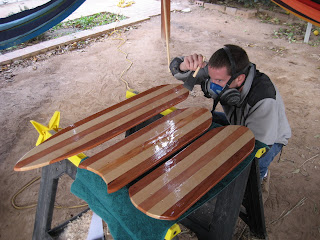
And now we play the waiting game... They sure are pretty while they're drying.